West End Workbench
Moderators: 52D, Tom F, Rlangham, Atlantic 3279, Blink Bonny, Saint Johnstoun, richard
-
- LNER A4 4-6-2 'Streak'
- Posts: 4303
- Joined: Wed Oct 25, 2006 8:46 am
Re: West End Workbench
Have to remember not to park it on the ramp up to the coal drops.
-
- LNER A4 4-6-2 'Streak'
- Posts: 4303
- Joined: Wed Oct 25, 2006 8:46 am
Re: West End Workbench
Completely vile day here today. In between picking my fence panels up from next door's garden, I braved the cold in the workshop and made this.
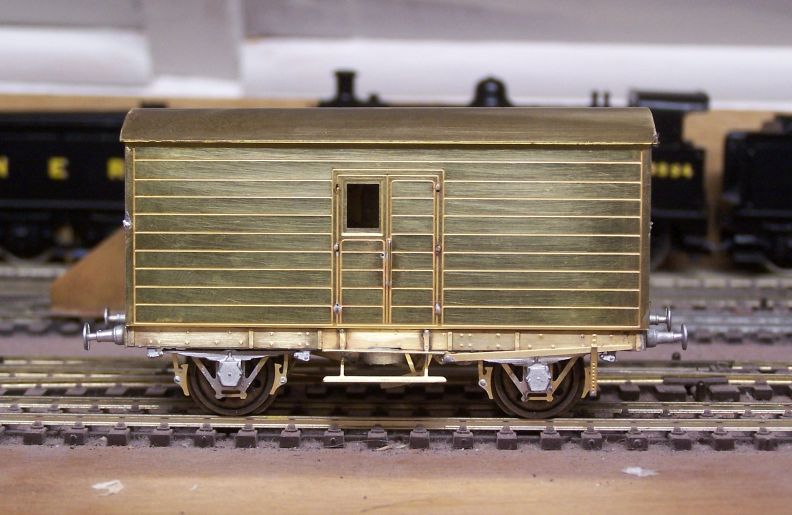
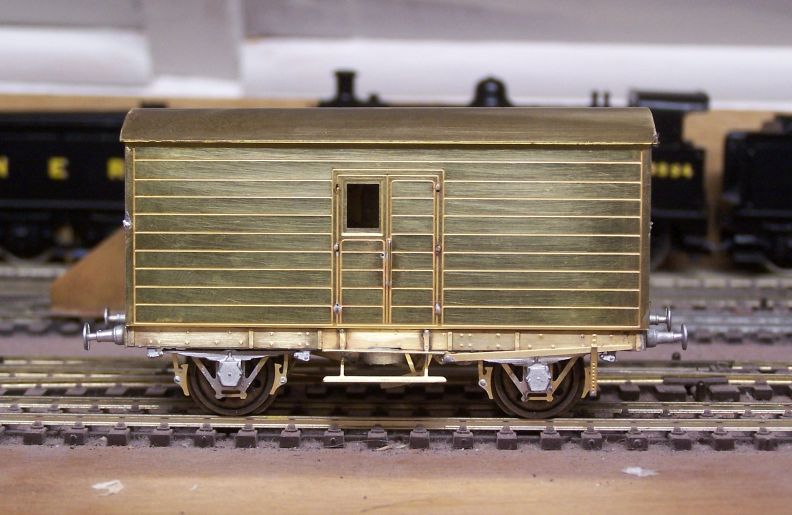
- manna
- LNER A4 4-6-2 'Streak'
- Posts: 3863
- Joined: Sun May 24, 2009 12:56 am
- Location: All over Australia
Re: West End Workbench
G'Day Gents
Are you burning the fence panels to keep warm ????
Come to Oz, 30c here today.......
manna
Are you burning the fence panels to keep warm ????
Come to Oz, 30c here today.......



manna
EDGWARE GN, Steam in the Suburbs.
-
- GNR C1 4-4-2
- Posts: 713
- Joined: Tue Nov 27, 2012 8:59 am
- Location: South Australia
Re: West End Workbench
Presume this is D&S kit?
-
- LNER A4 4-6-2 'Streak'
- Posts: 4303
- Joined: Wed Oct 25, 2006 8:46 am
Re: West End Workbench
It is. I'm not exactly sure which one, it was one of Danny's recent reissues and there were 3 kits in the same box. DS268, I think.
-
- GNR C1 4-4-2
- Posts: 713
- Joined: Tue Nov 27, 2012 8:59 am
- Location: South Australia
Re: West End Workbench
I got a DS 289 Dia 360 GN CCT a couple of years ago or more but it had an etch missing which included one side, end and detail bits. Not managed to get the missing parts from Dan yet.
- Chas Levin
- GER D14 4-4-0 'Claud Hamilton'
- Posts: 300
- Joined: Fri Apr 10, 2015 11:54 am
- Location: London
Re: West End Workbench
Very smart! I have one in the pile too, it has very simple, elegant proportions doesn't it?
Chas
-
- LNER A4 4-6-2 'Streak'
- Posts: 4303
- Joined: Wed Oct 25, 2006 8:46 am
Re: West End Workbench
Having opened the box, you have to finish them, don't you, or they go off? Or bits get lost or pinched for other jobs.
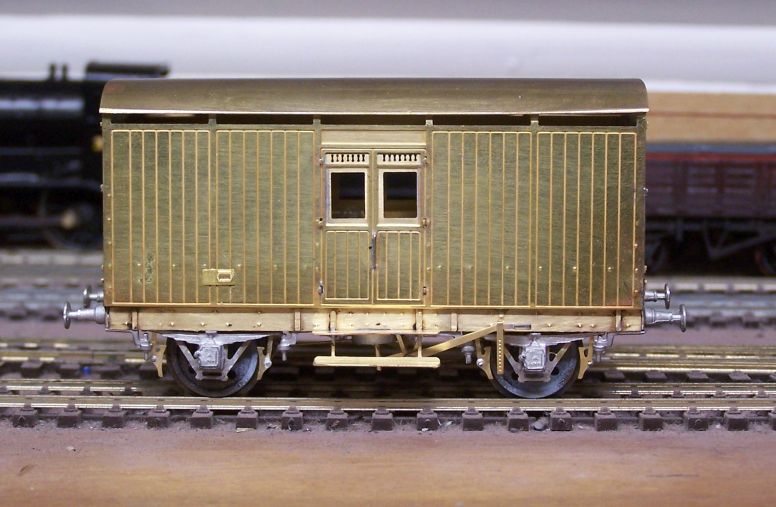
This is DS 289, which Andrew tells me is a D360 CCT. The one last week must be a D364 on that case. To be honest, this is the one I meant to build last weekend and then opened the wrong etch. The reason for that will become apparent in the next few weeks. This one took 2 hours less than the first, partly because it was much warmer and there were fewer stops to defrost and partly because the kits are all but identical and I didn't have to think so much about what I was doing.
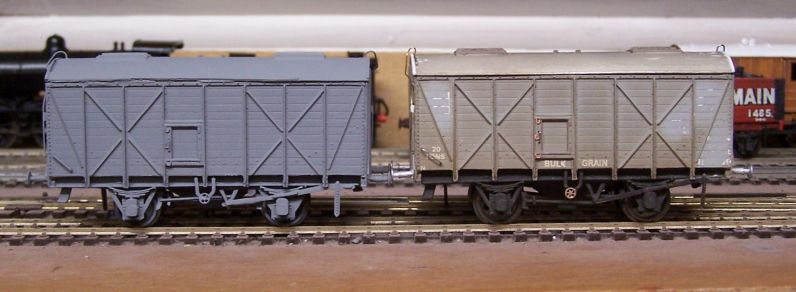
I've also been working on grain hoppers through the week; here one has had primer, one is ready for it.
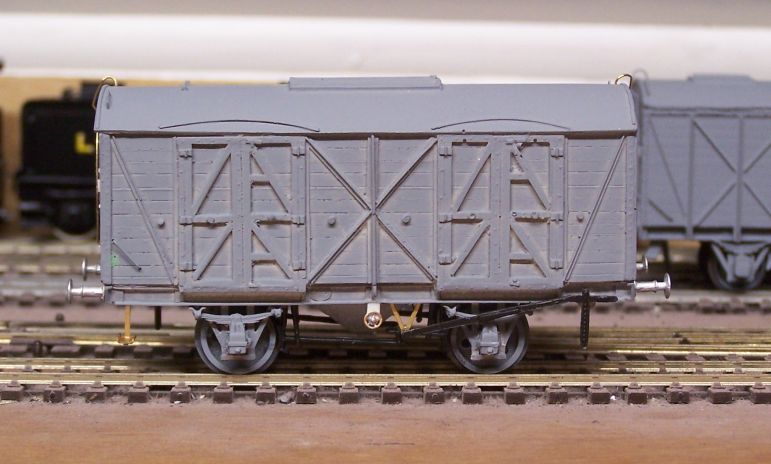
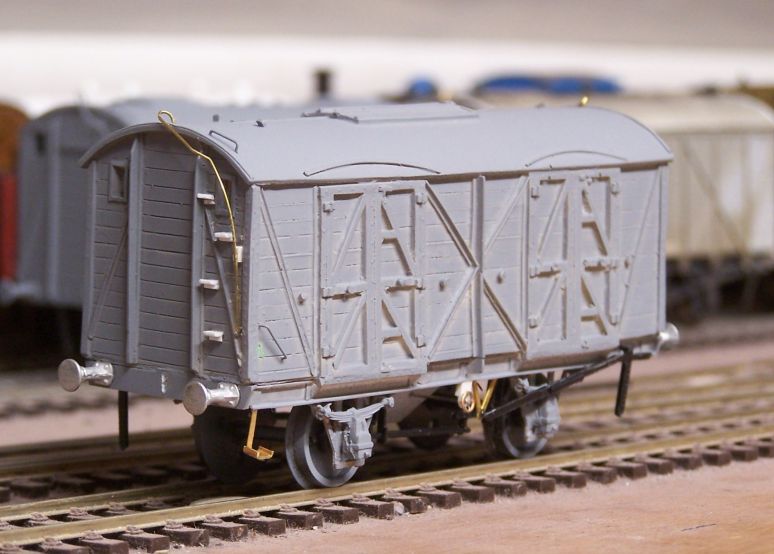
The resin one has taken most of the available time. I found some spare brake gear in the parts bin which saved some effort and the rest was really just a case of looking at Tatlow. I hadn't noticed, or had forgotten, that there's only one set of end steps on the master. Easy enough to make up. The steps are very vulnerable, it'll remain to be seen how they last. I've set them behind the solebar to try to get a better key and also make them less liable to catch anything. Only the very visible door locking mechanism to add now.
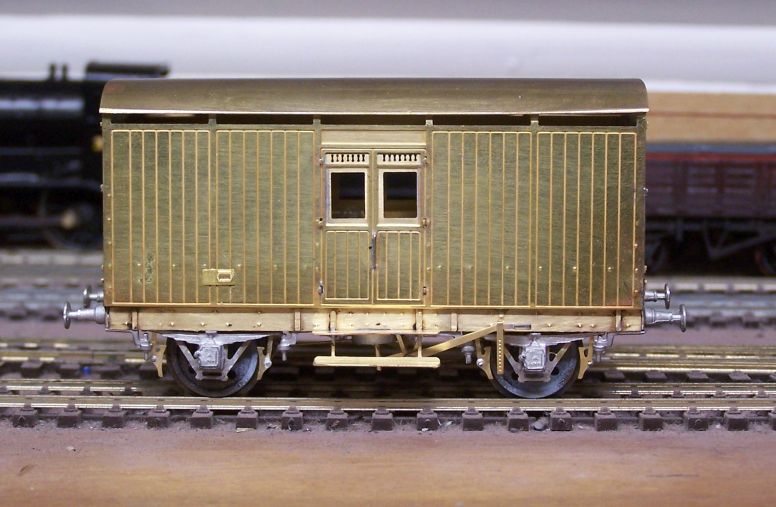
This is DS 289, which Andrew tells me is a D360 CCT. The one last week must be a D364 on that case. To be honest, this is the one I meant to build last weekend and then opened the wrong etch. The reason for that will become apparent in the next few weeks. This one took 2 hours less than the first, partly because it was much warmer and there were fewer stops to defrost and partly because the kits are all but identical and I didn't have to think so much about what I was doing.
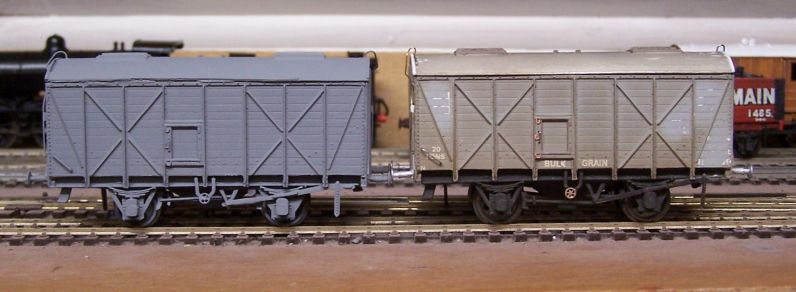
I've also been working on grain hoppers through the week; here one has had primer, one is ready for it.
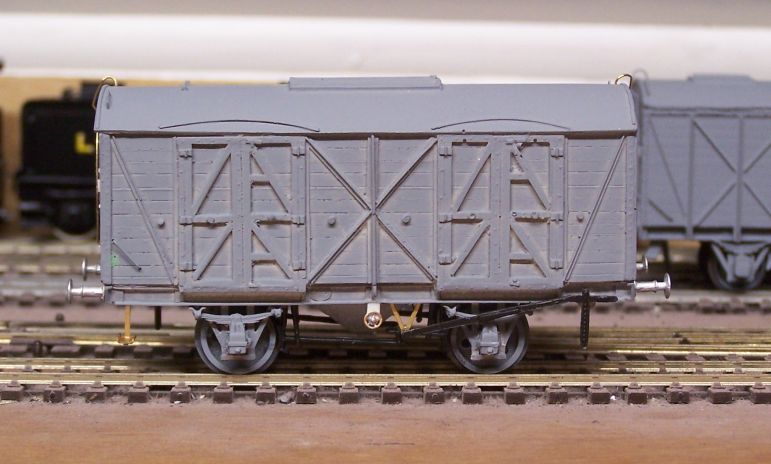
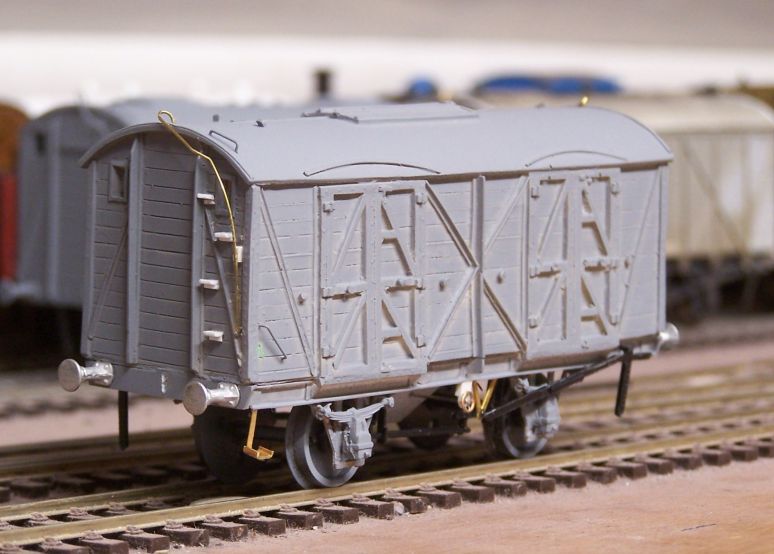
The resin one has taken most of the available time. I found some spare brake gear in the parts bin which saved some effort and the rest was really just a case of looking at Tatlow. I hadn't noticed, or had forgotten, that there's only one set of end steps on the master. Easy enough to make up. The steps are very vulnerable, it'll remain to be seen how they last. I've set them behind the solebar to try to get a better key and also make them less liable to catch anything. Only the very visible door locking mechanism to add now.
-
- LNER A4 4-6-2 'Streak'
- Posts: 4303
- Joined: Wed Oct 25, 2006 8:46 am
Re: West End Workbench
Grain hoppers are painted and awaiting transfers (on order from Powsides). In the meantime some more wagons came my way as birthday presents, so naturally I at once pulled them apart and started chopping them about....
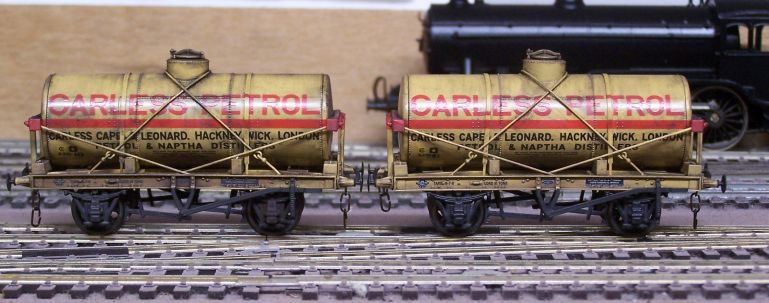
I'd seen pictures of the Oxford rail tank wagons and been impressed as well as hearing good reports from people who's opinion I'd take seriously. I have to say these are very good. I've done very little to these except complete the lettering over the strapping and fit Smiths couplings before weathering. They come with 3 link coupling loops but these are firmly closed so you can't use them with the Smiths hooks except by cutting them. I gather the Oxford hooks are functional, but I prefer the larger Smiths version.
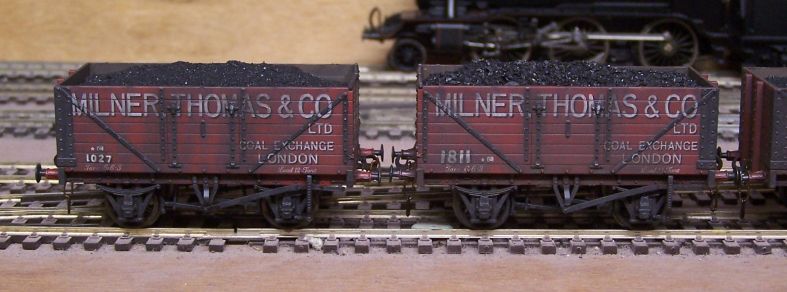
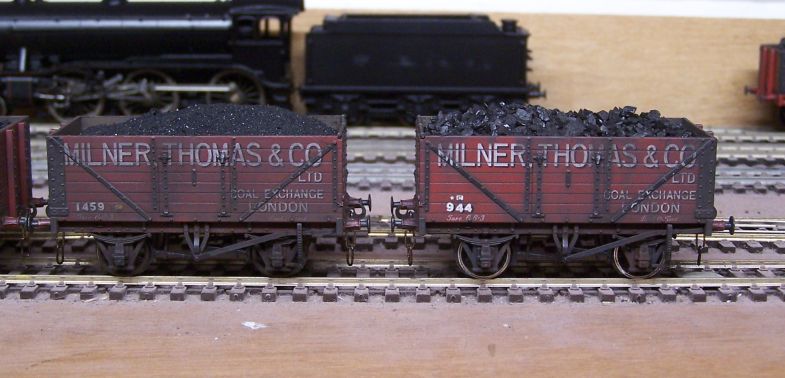
Oxford's 7 plank minerals have been criticised in these pages but they do make adequate layout vehicles and credit to them for producing liveries which no-one else seems to have done. I'd not seen this particular one before, but a set of 4 came my way. The incorrect capping strip clips have been removed, LMS buffers, Smiths couplings and renumbering.
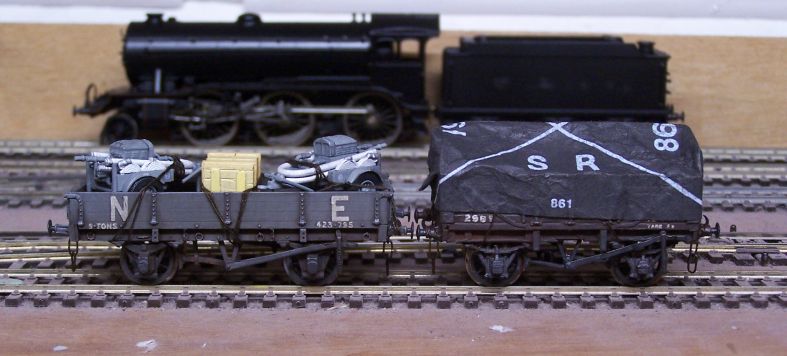
More Oxford, the Coventry Climax trailer pumps were also a nice little item which I'd seen used elsewhere. Matted down and with a dark wash they look very good. The crate by King's of Grimsby and the Colwick open which was looking for a load has been seen on these pages before. The LSWR open was in a job lot of wagons and had been scratchbuilt, probably in the 1970s if the date on another in the same lot is to be believed. The body shape was good but the brass strapping was awful - about 1.5mm wide, creased, with attempts at rivets randomly spaced and no attempt to chamfer or shape corners or joins. I did wonder about just binning it, but that goes very much against the grain so instead I repaired and reworked the bottom half and then applied a sheet as you see. It'll pass muster and can carry on running for another 40 years or however long the plastic lasts.
That leads me on to the next item. Joshua, Quicksilver95 of this parish, mentioned last summer that he'd created a kit of parts for a D 358 GNR CCT using a Silhouette cutter. I've seen Rob Pulham do this in 7mm, but hadn't seen anything in 4mm which had caught my fancy before that point. Anyway, after some correspondence Joshua kindly sent me a sheet of parts and it's been awaiting my attention since shortly before Christmas. I built the D & S ones first to become familiar with the prototype as there are no instructions and I haven't yet found a picture of this particular diagram. The first photographs are of the white plastic so apologies for the lack of contrast but hopefully you'll get the idea.
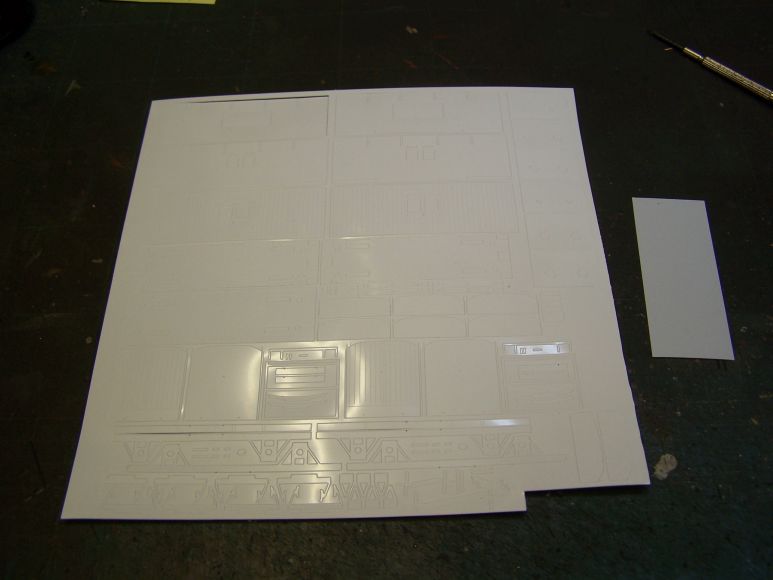
This is the sheet of parts as it arrived. The parts are scored into the (15 thou) sheet but need tracing round with a sharp knife then popping out. The roof was separate so I assume there's just a little too much for a single sheet.
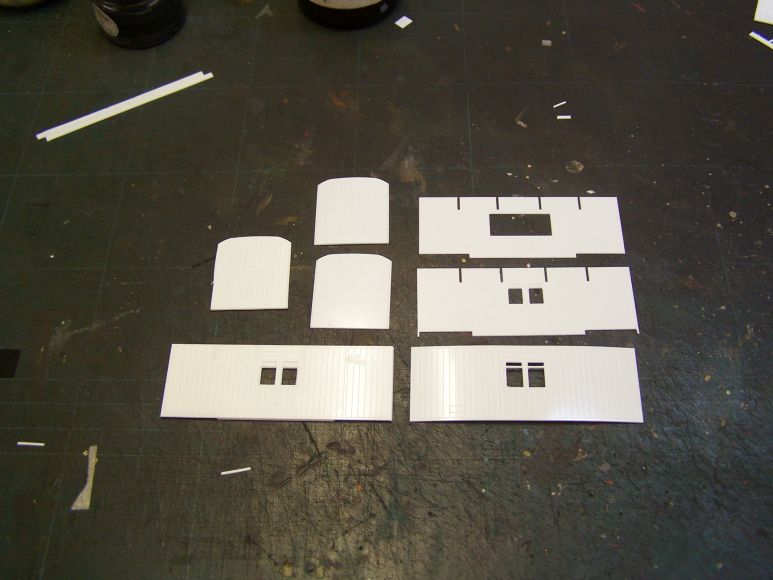
As you'd expect with plastic as thin as 20 thou, the parts all laminate together for strength. Here I've started with the easily identifiable bits, the sides and ends. To the right are the 3 layers of the sides, with a completed side on the left. Ends are above, two thicknesses to bind together. I used Limonene on all these parts and left them overnight under a weight to keep them flat.
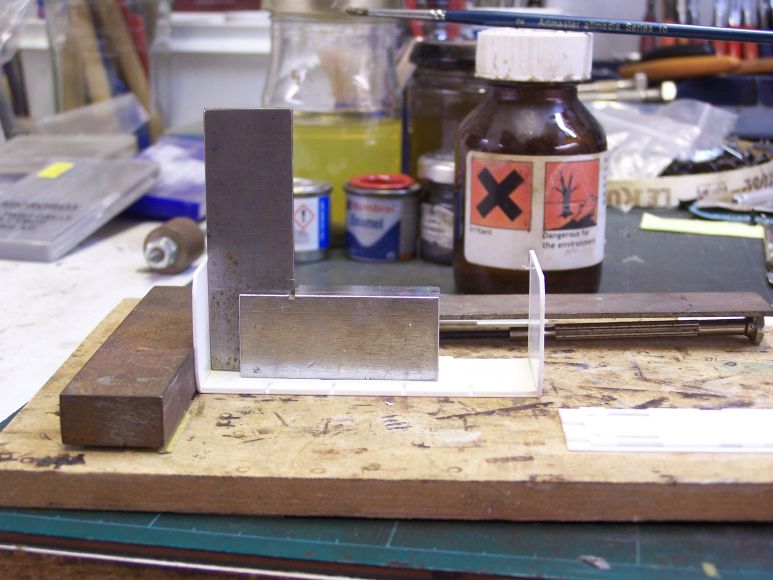
Here we're assembling the body against square blocks, again leaving 24 hours to dry at each step. The floor can be seen in the foreground, again 3 layers laminated together.
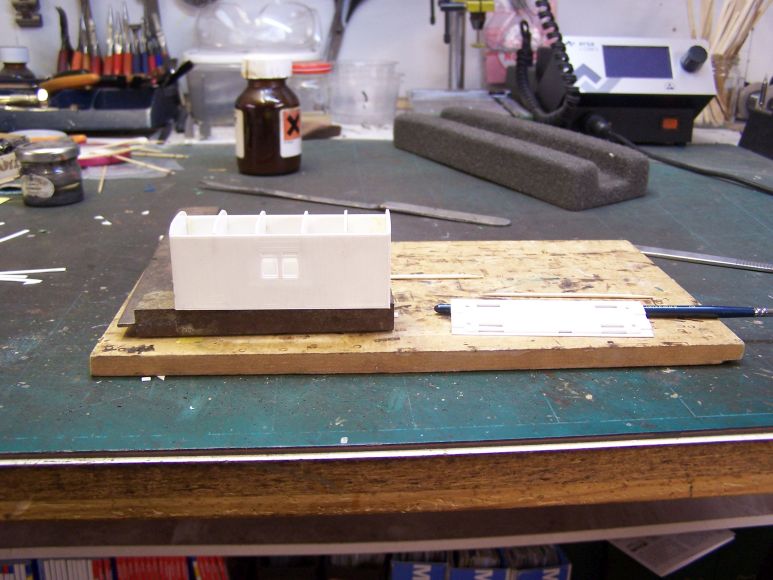
Finally the body, complete and with the roof formers stuck in to add rigidity. The floor, now the right way up, is to the right. Joshua has mirrored the D & S kit by designing this to split apart at the solebar. There are floor sections in the body with cut recesses for 8BA nuts and matching holes in the floor to pass screws up and secure the two together. It's now on wheels and has been primed, but the camera decided to screw up the last photo so you'll have to stay in suspense for a while.
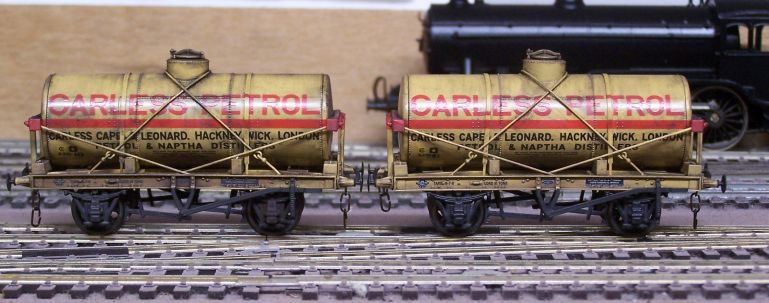
I'd seen pictures of the Oxford rail tank wagons and been impressed as well as hearing good reports from people who's opinion I'd take seriously. I have to say these are very good. I've done very little to these except complete the lettering over the strapping and fit Smiths couplings before weathering. They come with 3 link coupling loops but these are firmly closed so you can't use them with the Smiths hooks except by cutting them. I gather the Oxford hooks are functional, but I prefer the larger Smiths version.
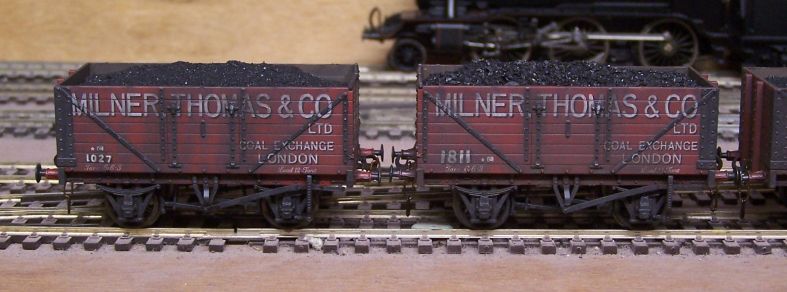
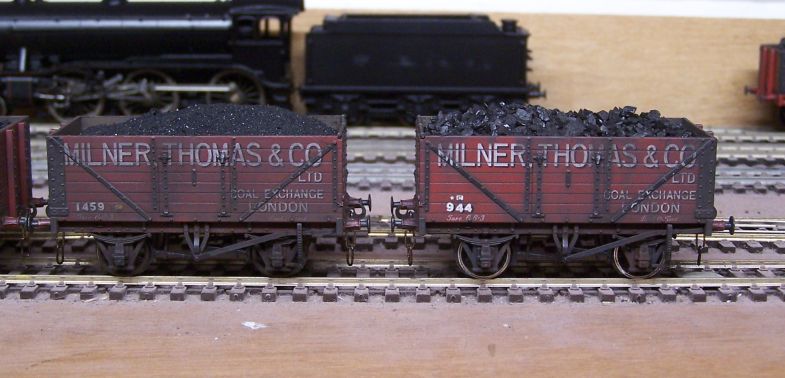
Oxford's 7 plank minerals have been criticised in these pages but they do make adequate layout vehicles and credit to them for producing liveries which no-one else seems to have done. I'd not seen this particular one before, but a set of 4 came my way. The incorrect capping strip clips have been removed, LMS buffers, Smiths couplings and renumbering.
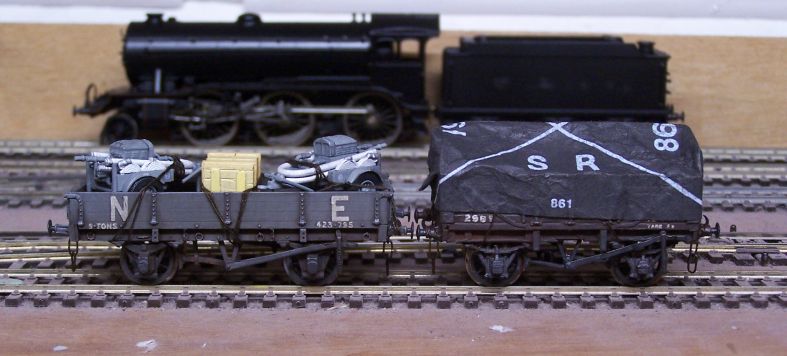
More Oxford, the Coventry Climax trailer pumps were also a nice little item which I'd seen used elsewhere. Matted down and with a dark wash they look very good. The crate by King's of Grimsby and the Colwick open which was looking for a load has been seen on these pages before. The LSWR open was in a job lot of wagons and had been scratchbuilt, probably in the 1970s if the date on another in the same lot is to be believed. The body shape was good but the brass strapping was awful - about 1.5mm wide, creased, with attempts at rivets randomly spaced and no attempt to chamfer or shape corners or joins. I did wonder about just binning it, but that goes very much against the grain so instead I repaired and reworked the bottom half and then applied a sheet as you see. It'll pass muster and can carry on running for another 40 years or however long the plastic lasts.
That leads me on to the next item. Joshua, Quicksilver95 of this parish, mentioned last summer that he'd created a kit of parts for a D 358 GNR CCT using a Silhouette cutter. I've seen Rob Pulham do this in 7mm, but hadn't seen anything in 4mm which had caught my fancy before that point. Anyway, after some correspondence Joshua kindly sent me a sheet of parts and it's been awaiting my attention since shortly before Christmas. I built the D & S ones first to become familiar with the prototype as there are no instructions and I haven't yet found a picture of this particular diagram. The first photographs are of the white plastic so apologies for the lack of contrast but hopefully you'll get the idea.
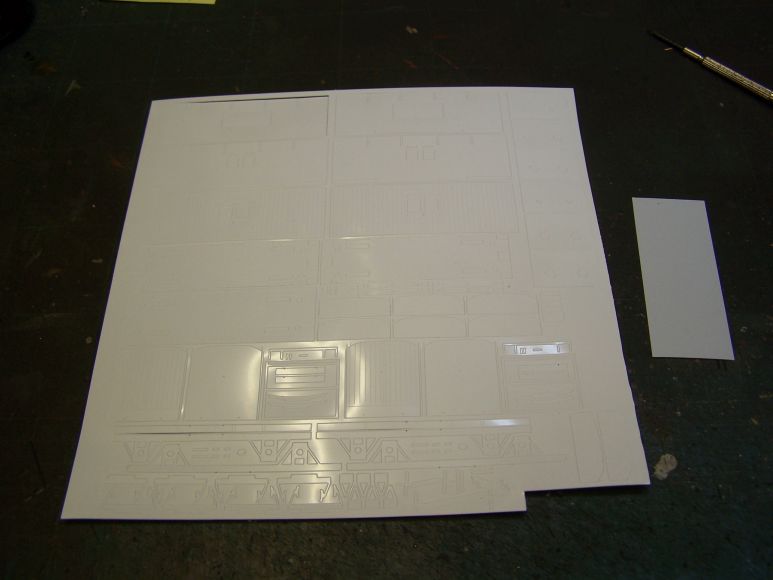
This is the sheet of parts as it arrived. The parts are scored into the (15 thou) sheet but need tracing round with a sharp knife then popping out. The roof was separate so I assume there's just a little too much for a single sheet.
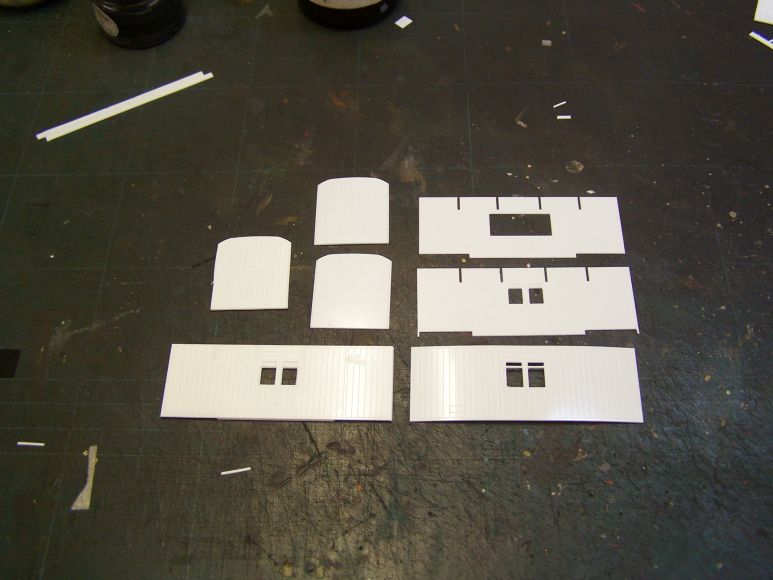
As you'd expect with plastic as thin as 20 thou, the parts all laminate together for strength. Here I've started with the easily identifiable bits, the sides and ends. To the right are the 3 layers of the sides, with a completed side on the left. Ends are above, two thicknesses to bind together. I used Limonene on all these parts and left them overnight under a weight to keep them flat.
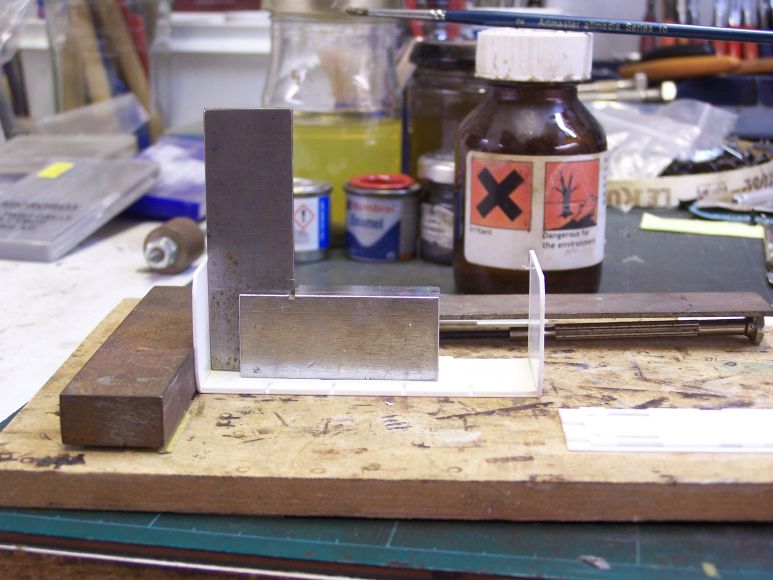
Here we're assembling the body against square blocks, again leaving 24 hours to dry at each step. The floor can be seen in the foreground, again 3 layers laminated together.
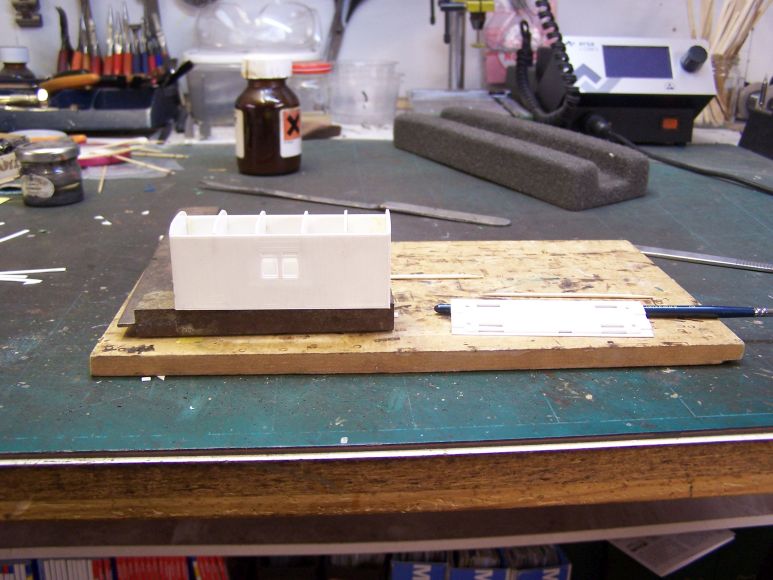
Finally the body, complete and with the roof formers stuck in to add rigidity. The floor, now the right way up, is to the right. Joshua has mirrored the D & S kit by designing this to split apart at the solebar. There are floor sections in the body with cut recesses for 8BA nuts and matching holes in the floor to pass screws up and secure the two together. It's now on wheels and has been primed, but the camera decided to screw up the last photo so you'll have to stay in suspense for a while.
Last edited by jwealleans on Sun Mar 14, 2021 3:57 pm, edited 1 time in total.
- Robpulham
- LNER A4 4-6-2 'Streak'
- Posts: 1721
- Joined: Thu Mar 27, 2008 9:54 pm
- Location: Lower Wensleydale
- Contact:
Re: West End Workbench
Nice to see more use being made of the Silhouette cutter and interesting to see how others design and tackle things.
I think that I will add one of these to my list when I get back to all things scratch built.
A couple of questions if I may, are the roof ribs laminated? I added them on my first design of an NER CCT but I only had a single 2o thou layer so they were not much use.
Secondly what are the cut outs at the bottoms of the inner sides for? Presumably to tie into the floor but it would be interesting to see how it was achieved.
I think that I will add one of these to my list when I get back to all things scratch built.
A couple of questions if I may, are the roof ribs laminated? I added them on my first design of an NER CCT but I only had a single 2o thou layer so they were not much use.
Secondly what are the cut outs at the bottoms of the inner sides for? Presumably to tie into the floor but it would be interesting to see how it was achieved.
-
- LNER A4 4-6-2 'Streak'
- Posts: 4303
- Joined: Wed Oct 25, 2006 8:46 am
Re: West End Workbench
Afternoon Rob,
The roof ribs are laminated but only to double thickness. I think it's an area Joshua is looking at again.
The cutouts in the sides are for a short section of floor, triple laminated, with round holes in the bottom layer then hexagonal ones in the next two to hold nuts in place. At least, that's how I interpreted them. I'll try to get upstairs again this evening and take another couple of photos so you can see how that works.
The roof ribs are laminated but only to double thickness. I think it's an area Joshua is looking at again.
The cutouts in the sides are for a short section of floor, triple laminated, with round holes in the bottom layer then hexagonal ones in the next two to hold nuts in place. At least, that's how I interpreted them. I'll try to get upstairs again this evening and take another couple of photos so you can see how that works.
-
- NER J27 0-6-0
- Posts: 131
- Joined: Mon Sep 03, 2012 1:24 pm
- Location: Leicestershire
Re: West End Workbench
Hi Jonathan,
Nice to see some photos of the progress, certainly looks like a neat job so far! Thanks for giving it a go, and I apologise for the lack of clear instructions! You are right in your assessment of the floor pieces. I'd had enough of trying to arbitrarily hold 8BA nuts in place on a plastic model, so that was an area I've sought to use the benefits of the silhouette cutter. I have found a small dab of super glue is usually sufficient to hold them in place.
Regarding the roof, I'm still not 100% satisfied with how I've set things up. I'm currently using a sheet of 10thou, which I pre-roll to give a general curvature, then secure to the roof ribs to give the correct shape. I'm happy that the transverse ribs are strong enough to produce the correct form, but I've found that there is still some degree of "sag" between each rib. Ideally I need some more longitudinal supports, so I may produce a series of ribs that run the length of the body and help to support the roof. These could slot into the ribs and also recess into one layer at the ends.
I should add that all the plastic in the kit except the roof is 15thou. Slightly less frequently sold, but I find it is the maximum thickness that the Silhouette Portrait will cut, and provides about the best compromise between being able to provide fine details but not so fine as to be too flimsy.
I've been experimenting with trying to produce as many aspects of a kit as possible using sheet plasticard. I'm aware that it may not be always the best choice for every component, but it certainly helps to bring the cost per vehicle down! Some of the bits I've (attempted to) produce for the underframe are probably on the flimsier and coarser side, and would be better suited to brass or white metal, but I'm enjoying the experiment of pushing the Silhouette cutter to its limits. I've learned a lot on this one, and have subsequently used the same techniques, with some improvements, to produce an LNER ballast brake (see my thread). Wondering what I might tackle next. One of the benefits of the silhouette would be that I could produce a lot of similar vehicles very quickly, but so far my two chosen prototypes have been quite limited in their numbers! Suggestions welcome!
Thanks,
Joshua
Nice to see some photos of the progress, certainly looks like a neat job so far! Thanks for giving it a go, and I apologise for the lack of clear instructions! You are right in your assessment of the floor pieces. I'd had enough of trying to arbitrarily hold 8BA nuts in place on a plastic model, so that was an area I've sought to use the benefits of the silhouette cutter. I have found a small dab of super glue is usually sufficient to hold them in place.
Regarding the roof, I'm still not 100% satisfied with how I've set things up. I'm currently using a sheet of 10thou, which I pre-roll to give a general curvature, then secure to the roof ribs to give the correct shape. I'm happy that the transverse ribs are strong enough to produce the correct form, but I've found that there is still some degree of "sag" between each rib. Ideally I need some more longitudinal supports, so I may produce a series of ribs that run the length of the body and help to support the roof. These could slot into the ribs and also recess into one layer at the ends.
I should add that all the plastic in the kit except the roof is 15thou. Slightly less frequently sold, but I find it is the maximum thickness that the Silhouette Portrait will cut, and provides about the best compromise between being able to provide fine details but not so fine as to be too flimsy.
I've been experimenting with trying to produce as many aspects of a kit as possible using sheet plasticard. I'm aware that it may not be always the best choice for every component, but it certainly helps to bring the cost per vehicle down! Some of the bits I've (attempted to) produce for the underframe are probably on the flimsier and coarser side, and would be better suited to brass or white metal, but I'm enjoying the experiment of pushing the Silhouette cutter to its limits. I've learned a lot on this one, and have subsequently used the same techniques, with some improvements, to produce an LNER ballast brake (see my thread). Wondering what I might tackle next. One of the benefits of the silhouette would be that I could produce a lot of similar vehicles very quickly, but so far my two chosen prototypes have been quite limited in their numbers! Suggestions welcome!
Thanks,
Joshua
- Robpulham
- LNER A4 4-6-2 'Streak'
- Posts: 1721
- Joined: Thu Mar 27, 2008 9:54 pm
- Location: Lower Wensleydale
- Contact:
Re: West End Workbench
See later post
Last edited by Robpulham on Mon Mar 15, 2021 12:05 am, edited 1 time in total.
- Robpulham
- LNER A4 4-6-2 'Streak'
- Posts: 1721
- Joined: Thu Mar 27, 2008 9:54 pm
- Location: Lower Wensleydale
- Contact:
Re: West End Workbench
Thanks Jonathan,jwealleans wrote: ↑Sun Mar 14, 2021 1:50 pm Afternoon Rob,
The roof ribs are laminated but only to double thickness. I think it's an area Joshua is looking at again.
The cutouts in the sides are for a short section of floor, triple laminated, with round holes in the bottom layer then hexagonal ones in the next two to hold nuts in place. At least, that's how I interpreted them. I'll try to get upstairs again this evening and take another couple of photos so you can see how that works.
- Robpulham
- LNER A4 4-6-2 'Streak'
- Posts: 1721
- Joined: Thu Mar 27, 2008 9:54 pm
- Location: Lower Wensleydale
- Contact:
Re: West End Workbench
Hi Joshua,
You might try using 15 or 20 thou for the roof but scoring horizontal plank lines the length of the roof. This technique really helps to make the roof curve if you leave the cut marks to the outside it curves naturally as you take it off the cutting mat. This makes the roof much more rigid lengthwise so you may not need addition longitudinal ribs
If you then cover the roof with tissue, the cut lines are not visible on the finished model. It works fine in 7mm scale so I see no reason why it wouldn't work in 4mm.
You might try using 15 or 20 thou for the roof but scoring horizontal plank lines the length of the roof. This technique really helps to make the roof curve if you leave the cut marks to the outside it curves naturally as you take it off the cutting mat. This makes the roof much more rigid lengthwise so you may not need addition longitudinal ribs
If you then cover the roof with tissue, the cut lines are not visible on the finished model. It works fine in 7mm scale so I see no reason why it wouldn't work in 4mm.