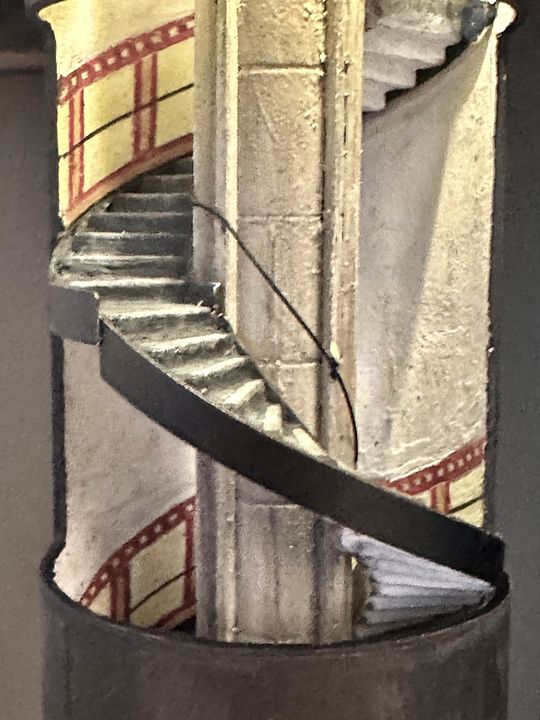
The construction was aided by John Jesson producing laser cut step sections using the MRC laser-cutting facility; rather like a castle stairway (the top step shows the profile).
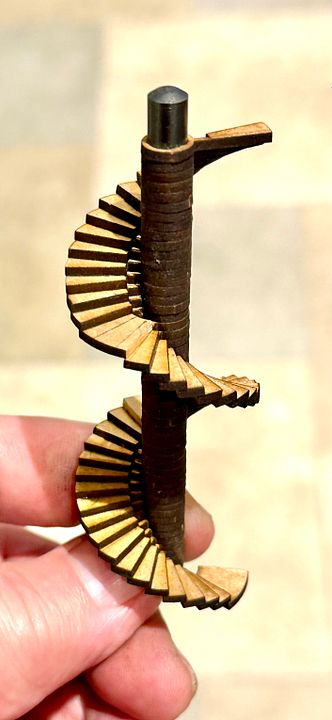
Once glued together, the centre section was cut away, the steps trimmed with a high speed tungsten carbide trimmer and a new brass ventilation shaft turned up to the correct diameter, complete with plate work jounts scribed into place. The aluminium collar helps to centralise and support the stairs towards the bottom. The reason for the polished conical tip will become apparent later (it’s not an ICBM).
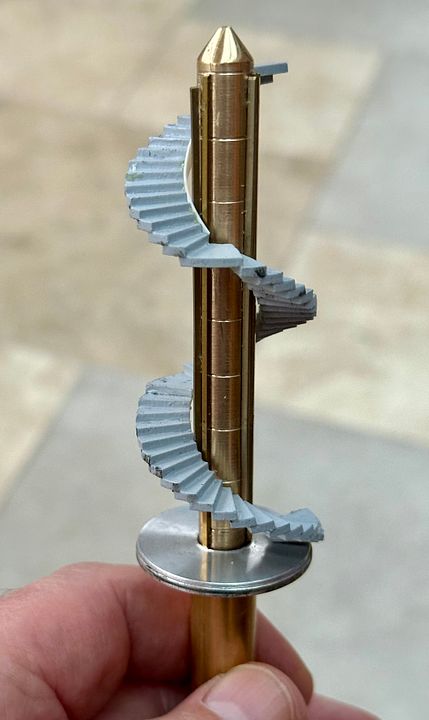
The copper pipe of the stair shaft had a window cut into it using diamond discs and the position of the stairs was then determined.
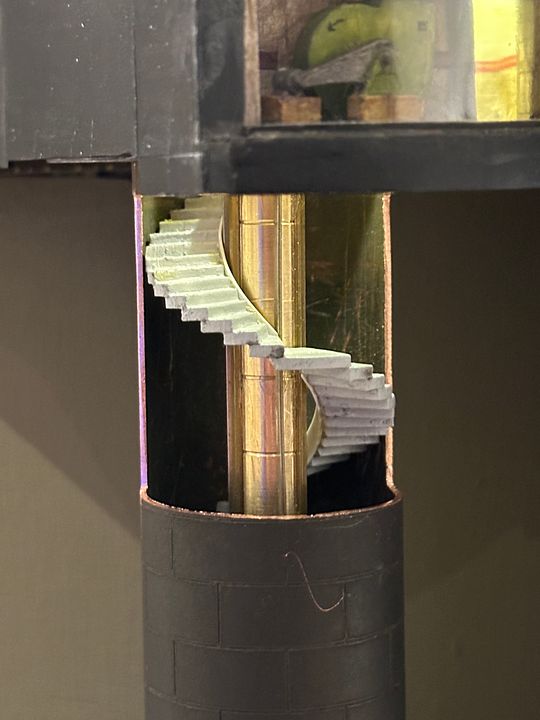
There are a number of conduits surrounding the ventilation shaft and these were represented by brass square section and strip. The vertical plate joints were scribed in using a tool in the lathe, where they would be conspicuous.
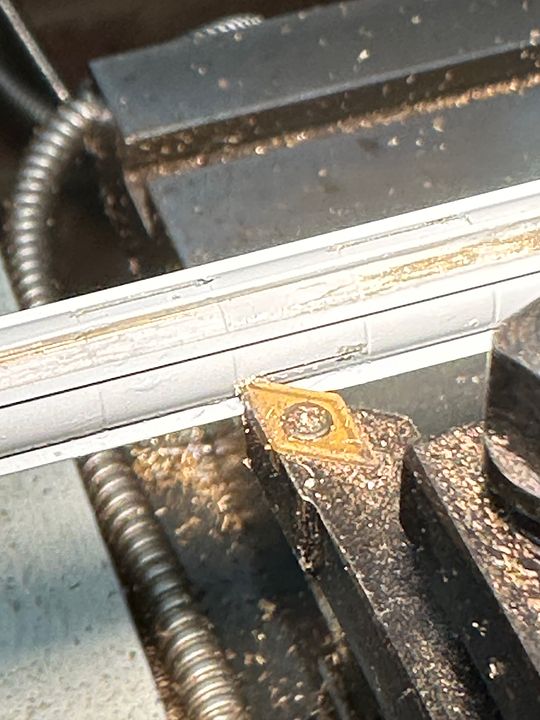
The artwork for the tiles was already available from the station building. Tile strips were cut out and thinned down from behind with a scalpel and tweezers so that they were almost like a transfer.
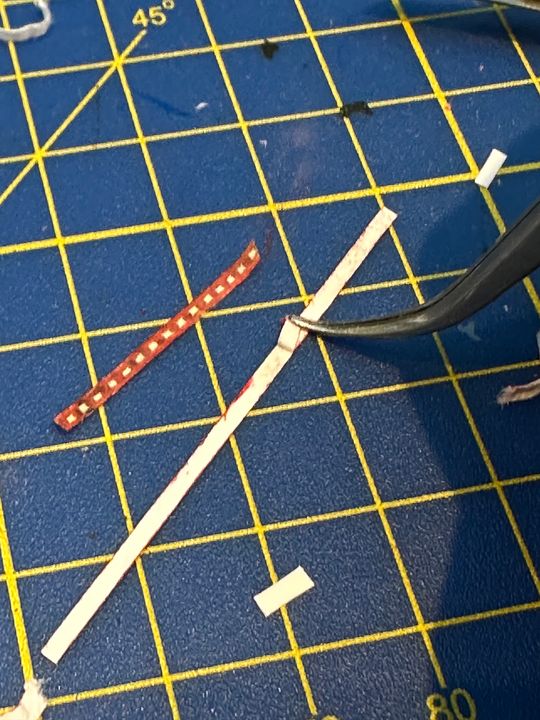
A paper liner was marked up and the individual tile patterns glued into place. I’m sure some clever person could have drawn all this up and printed it, but I’m more of a make it directly sort of person.
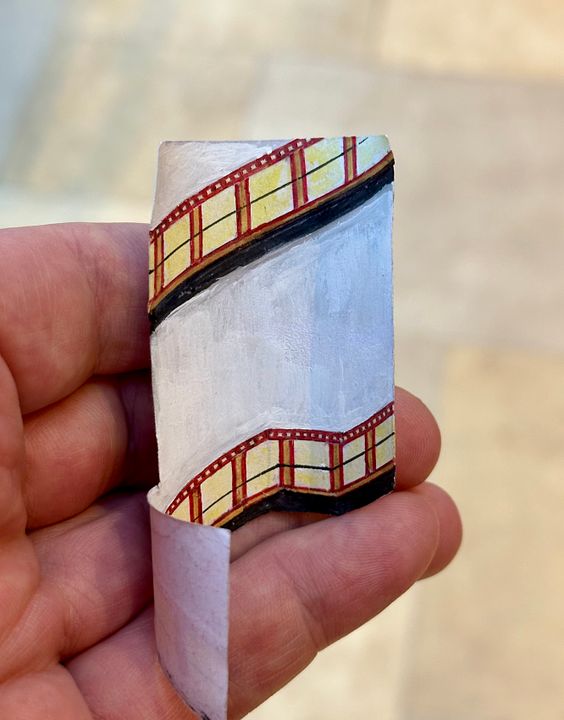
The liner was held in place with photo mount and a chrome metallic pen used to finish the top of the ventilation shaft cone and the top of the main shaft lining. Finally a light cured resin spherical lens was made to go on top of the cone. The reason for this? There is an LED positioned immediately above the main shaft in the roof and these reflective / refractive devices might capture and improve light transmission down the stairwell. I did not want to fiddle with extra LEDS.
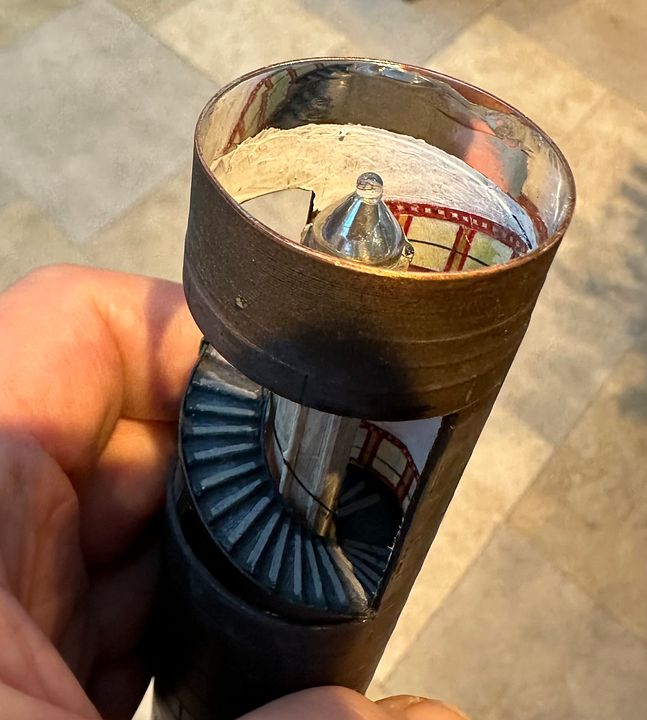
The final scene fulfils the aim we had three years ago of showing how a tube station is laid out. It’s not really realistic modelling, but I’ve found it great fun to do.
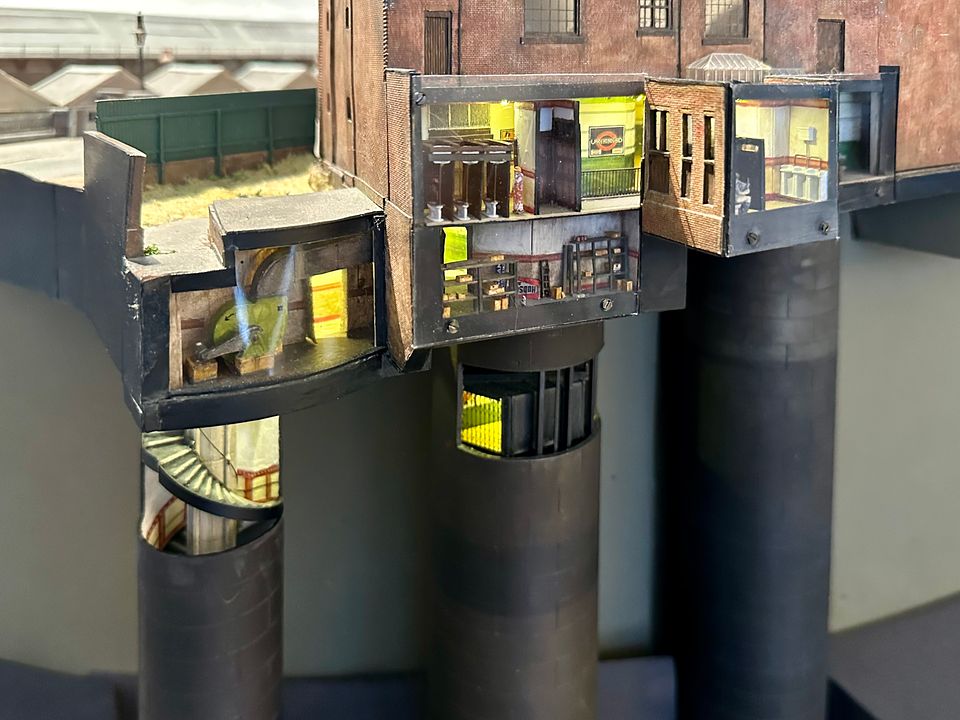
Just for completeness here is a
link showing the famous Covent Garden steps. https://www.reddit.com/media?url=https% ... 67d3bf2a61
I think that’s enough tube modelling for a while, apologies for the long post!
Tim